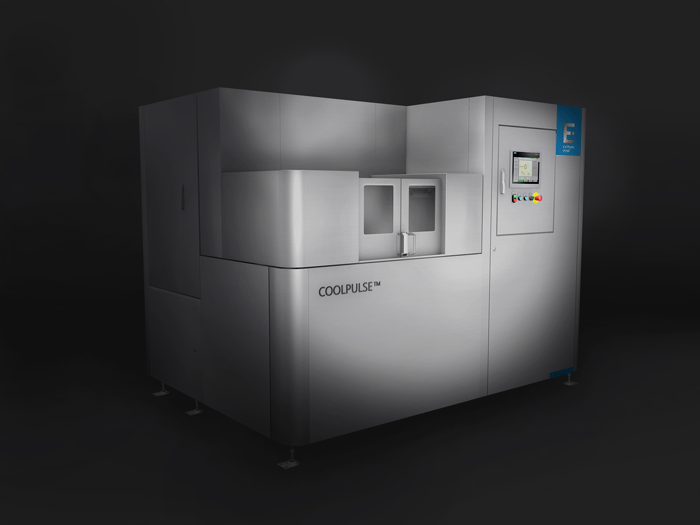
Extrude Hone at the Paris Air Show Hall H3 Booth D29
AFM, MICROFLOW, and COOLPULSE™ finishing solutions for inner and outer metal 3D printed component surfaces.
For many years Extrude Hone has helped the aerospace industry to improve surfaces.
Now Extrude Hone continues that mission to address the new challenges surrounding 3D printed components.
Surface improvement for metal 3D printed parts is always a challenge and getting the right solution brings a component within the realms of being truly functional.
Freedom of design is a key benefit of using 3D printing but at the same time it’s generating new challenges regarding surface improvement.
Intricate inner passages and/or complex outer surfaces with demanding roughness improvement requirements recently became daily business at Extrude Hone.
A dedicated team focuses on 3D printed parts and integrates our different solutions to satisfy customer needs.
Traditional AFM is one of the best solutions to clean and improve the roughness of small channels.
As straight intersections and dead holes have been replaced in 3D printed parts with convoluted passages requiring advanced surface improvement, AFM becomes an even more interesting solution.
When holes get smaller (down to the size of injection spray holes) we have another solution called MICROFLOW that will deliver flow calibration within tight flow tolerances.
To address external surface finishing, alternative to the AFM process, we launched during our Technology Days in May 2017: COOLPULSE™.
COOLPULSE™ is much more than just a machine or a process it’s a global concept with digitalization at its core.
We use the customer’s workpiece CAD file to design an optimized cathode or set of cathodes that will also be printed (metal or plastic with coating). At the same time, depending on the material to be processed and the requirements, we define a set of dedicated parameters.
The cathodes and the part are connected effortlessly to the COOLPULSE™ machine, thanks to a patented system. Production parameters are loaded remotely to the machine and the workpiece is processed creating a defined surface structure at both macro and micro level.
Flexibility is key. Either the customer or Extrude Hone can build the cathode and the processing of the part can be done by the customer (if equipped with a COOLPULSE™ machine) or in one of our Extrude Hone Contract Shops.
Some finishing operations could be optimized by combining the different processes, such as processing inner and outer surfaces of a part using a different technology or by combining both technologies on the same surface, depending on the requirements.
See you at the Paris Air Show.