Le giranti chiuse svolgono un ruolo fondamentale in diverse applicazioni industriali e sono componenti chiave nei processi di conversione dell’energia. Definite da un rivestimento interno ed esterno attorno alle palette, queste giranti hanno un impatto significativo sull’efficienza e sul trasferimento di energia. Scoprite come le tecniche di finitura influiscono sulle prestazioni delle giranti chiuse.
Ottimizzazione delle prestazioni delle pompe grazie alla Finitura di alta qualità di giranti chiuse centrifughe
DIVERSI TIPI DI GIRANTI
Vediamo innanzitutto alcune nozioni di base sulle giranti. I design delle giranti si dividono in tre categorie:
GIRANTI CHIUSE
Sono dotati di protezioni interne ed esterne (lato aspirazione) intorno alle palette. Sono tipicamente utilizzate in applicazioni prive di solidi. Una girante chiusa, con palette singole o multiple, è strutturalmente superiore a una di tipo aperto. Pertanto, aumenta la durata della pompa.
GIRANTI SEMIAPERTE
Rispetto alla categoria precedente, sono dotati di una parete posteriore, il mantello interno, che rafforza la girante. Possono accogliere solidi in sospensione, ma con un’efficienza ridotta.
GIRANTI APERTE
Sono dotate di palette aperte su entrambi i lati e fissate al mozzo, ampiamente utilizzate in pompe e pompe piccole ed economiche. Sono inoltre comuni nelle applicazioni che richiedono di accogliere i solidi in sospensione.
PRODUZIONE DI GIRANTI CHIUSE
La maggior parte delle applicazioni può essere affrontata con materiale in ghisa grigia. Se vengono trattati fluidi aggressivi o corrosivi, è necessario prendere in considerazione altri materiali. Leghe e rivestimenti specifici possono essere utilizzati per migliorare la durata della girante contro i fluidi corrosivi.
PROCESSO DI PRODUZIONE DELLE GIRANTI CHIUSE
I materiali utilizzati per la produzione di giranti includono ghisa, acciaio, acciaio inossidabile, bronzo e talvolta plastica. Il processo di produzione prevede diverse fasi cruciali, a partire dalla progettazione precisa del modello utilizzando un software di progettazione assistita da computer (CAD) per creare modelli ottimizzati per i requisiti specifici dell’applicazione.
I processi di produzione comprendono la fusione convenzionale, la microfusione, la lavorazione, la saldatura, la sinterizzazione e la produzione additiva.
Si vedano questi due interessanti articoli sull’utilizzo del processo di fabbricazione additiva per la costruzione di giranti chiuse :
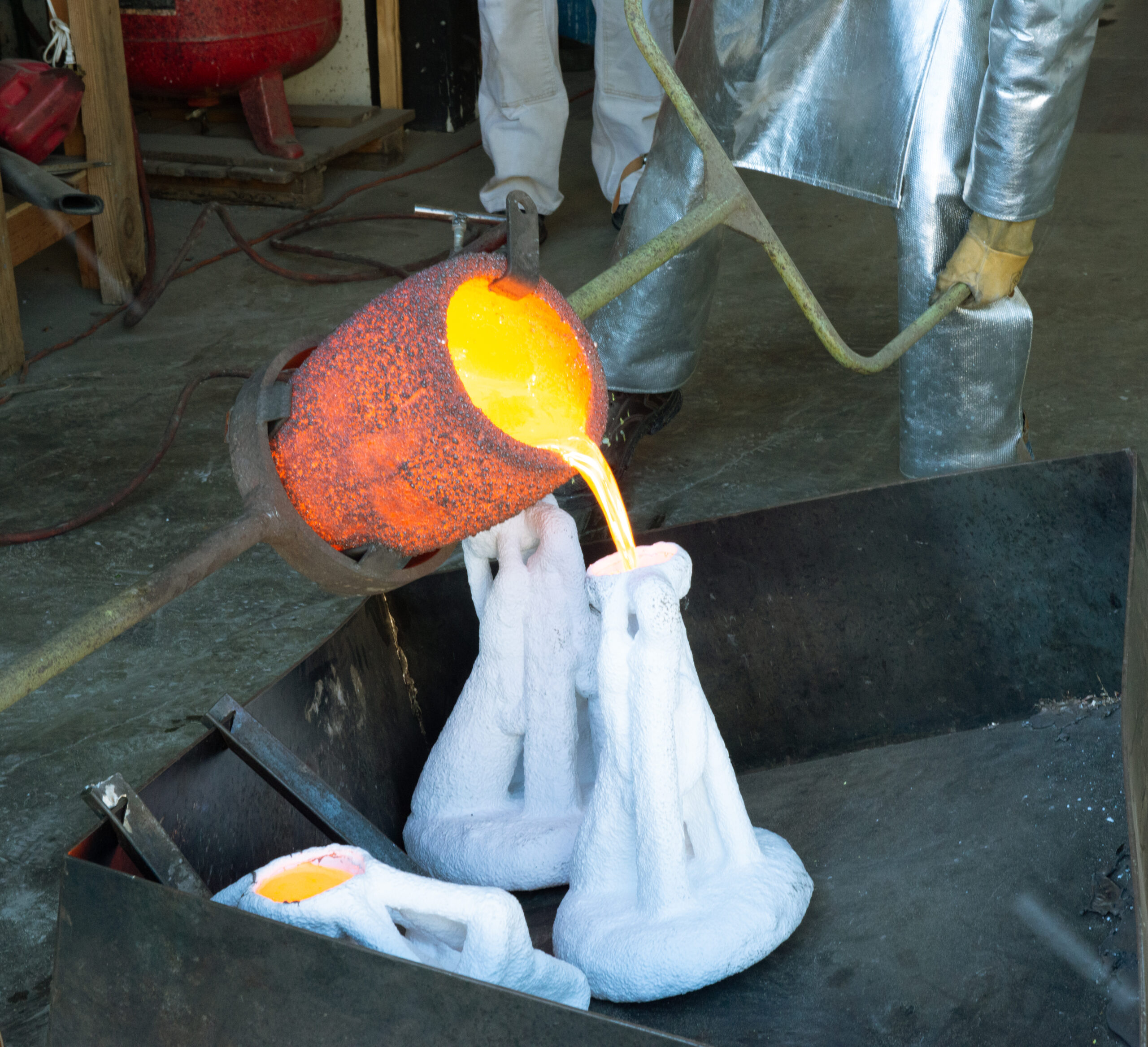
PRESSIONE E PORTATA : PARAMETRI DI PROGETTAZIONE FONDAMENTALI
La scelta di una pompa centrifuga richiede la considerazione della curva della pompa. Il grafico mostra prima e dopo il processo di lavorazione del flusso di abrasivo Extrude Hone:
- la portata (in m3/h) sull’asse orizzontale,
- la prevalenza (in metri) su quello verticale
- e la curva di efficienza in %.
L'INFLUENZA SULLA PRESSIONE :
La velocità e il diametro della girante determinano la pressione massima della pompa. L’altezza delle pale contribuisce alla portata gestita dalla pompa.
Il diametro può essere relativamente piccolo in alcune pompe per piscine, ma può arrivare a 2000 mm per i compressori LNG. Il diametro maggiore produce la portata/prevalenza più elevata.
IMPORTANZA DEL FLUIDO NEL FUNZIONAMENTO EFFICIENTE DELLA GIRANTE :
Il tipo di girante dipende dal fluido trattato: più è aperta, più è favorevole a liquidi ad alta viscosità, con particelle solide. Una girante chiusa, invece, è adatta a liquidi puliti e a bassa viscosità.
Le giranti chiuse sono più efficienti di quelle aperte, in quanto la loro testa di aspirazione positiva netta (NPSH) è inferiore.
LA FINITURA DEI PEZZI : UNA CARATTERISTICA ESSENZIALE NELLA PRODUZIONE DI GIRANTI
RUOLO DEL MIGLIORAMENTO DELLA SUPERFICIE NEL MIGLIORARE LE PRESTAZIONI DELLE GIRANTI
Un altro fattore critico per aumentare le prestazioni della pompa è la rugosità superficiale della girante.
Migliore è la rugosità della superficie, maggiore è l’efficienza meccanica e idraulica. Un flusso laminare migliore significa meno turbolenza, nessuna cavitazione, meno o nessuna bolla e nessuna caduta di pressione.
Una pompa centrifuga beneficerà di un funzionamento più fluido e di un minor consumo energetico.
Inoltre, il miglioramento della superficie elimina i residui positivi del processo di microfusione e garantisce una rimozione uniforme del materiale.
L'ACCURATA FINITURA RIDUCE LA RESISTENZA IDRODINAMICA
La lucidatura della superficie delle palette migliora l’efficienza della pompa, richiede meno energia o eroga di più a un determinato livello.
In un mondo sempre più incentrato sull’energia elettrica, ogni percentuale di efficienza guadagnata va a vantaggio del pianeta, attenua il cambiamento climatico e favorisce il vostro budget o quello del vostro cliente.
In conclusione, una buona finitura influisce sulle prestazioni delle giranti chiuse.
PROCESSO DI FINITURA A GIRANTI CHIUSE
MODERNE TECNICHE DI FINITURA: LUCIDATURA, RIVESTIMENTI SPECIALI, LAVORAZIONE A FLUSSO ABRASIVO
Per migliorare la rugosità superficiale della girante centrifuga sono disponibili diversi metodi di finitura. Tra questi, la lucidatura a mano, la vibrazione, la lavorazione e la sabbiatura. Diversi pro e contro da valutare:
- il costo,
- l’accesso alla manodopera
- e l’omogeneità del risultato.
Se il fluido che trattate è aggressivo a causa di solidi, temperatura elevata o carico chimico, ciò contribuirà a prolungarne la durata.
La lucidatura di intricati progetti di palette con superfici di visione fuori linea su giranti chiuse sta diventando sempre più difficile da realizzare. Fortunatamente, esiste una soluzione in cui la complessità del progetto diventa un vantaggio: la lavorazione a flusso abrasivo (AFM).
LAVORAZIONE A FLUSSO ABRASIVO - AFM, LA SOLUZIONE MIGLIORE PER LE GIRANTI CHIUSE
Si tratta della lavorazione a flusso abrasivo (Abrasive Flow Machining, AFM), in cui un mezzo elastico viscoso, caricato con grani abrasivi, si muove avanti e indietro attraverso le palette in un’unica operazione, ottenendo un miglioramento costante della superficie. Per trattenere la girante durante la lavorazione AFM è necessario un’attrezzatura.
L’attrezzatura dirige il materiale nell’area di lavoro e contribuisce a creare restrizioni artificiali nell’area di apertura delle palette per garantire un miglioramento omogeneo della superficie.
L’AFM viene utilizzato come processo ripetibile per affrontare i passaggi interni dei percorsi di flusso del fluido chiusi. Il cliente ha bisogno di migliorare drasticamente la rugosità, a volte fino a 10 volte. Possiamo fornire una rugosità finale compresa tra Ra0,8µm e Ra0,2µm, a seconda delle condizioni della superficie di partenza.
L’AFM è in grado di migliorare la rugosità della superficie pur rimanendo all’interno della tolleranza dello spessore della paletta. L’applicazione AFM è adatta anche per le giranti realizzate in AM.
SERVIZI E MACCHINE PER LA FINITURA DEGLI ESTRUSI
Se il vostro volume di produzione non giustifica un investimento, potreste essere interessati al nostro servizio di Contract Shop.
Inoltre, la nostra rete globale di assistenza Contract Shop vi fornirà un supporto esteso a domicilio. In Extrude Hone, in base alle dimensioni della girante chiusa, risponderemo alle vostre esigenze con una macchina AFM:
- ONE-WAY FLOW (cilindro di supporto 250 mm),
- EASYFLOW (cilindro di supporto fino a 250 mm),
- VECTOR (cilindro di supporto fino a 300 mm),
- o SPECTRUM (cilindro di supporto fino a 600 mm).
Potreste essere un OEM, un’azienda di revisione, una fonderia o un utente finale; le soluzioni Extrude Hone possono risolvere il problema:
- Miglioramento radicale della produttività,
- nessun ciclo di rilavorazione rispetto alla lucidatura manuale,
- supporto di progetti complessi
Se volete superare i rivali o migliorare il vostro prodotto, AFM by Extrude Hone manterrà la promessa.
I nostri esperti del Centro di eccellenza per la lavorazione a flusso abrasivo di Irwin, PA, USA, sono pronti a condividere la loro esperienza e le loro soluzioni.
STUDI DI CASO
Per saperne di più sulla nostra esperienza di finitura.
MAGGIORE EFFICIENZA DELLA POMPA CON LA LAVORAZIONE A FLUSSO ABRASIVO
L’efficienza delle pompe è importante
TECNOLOGIE DI FINITURA PER COMPONENTI A STRATI ADDITIVI.
La produzione additiva non è più solo uno strumento di prototipazione
PROGETTO ESA – INCDT – COMOTI
La lavorazione a flusso abrasivo (AFM) è stata necessaria per migliorare una girante chiusa progettata per sistemi a circuito fluido a pompaggio meccanico (MPFL).
SOLUZIONI DI EXTRUDE HONE
EXTRUDE HONE VICINO A ME
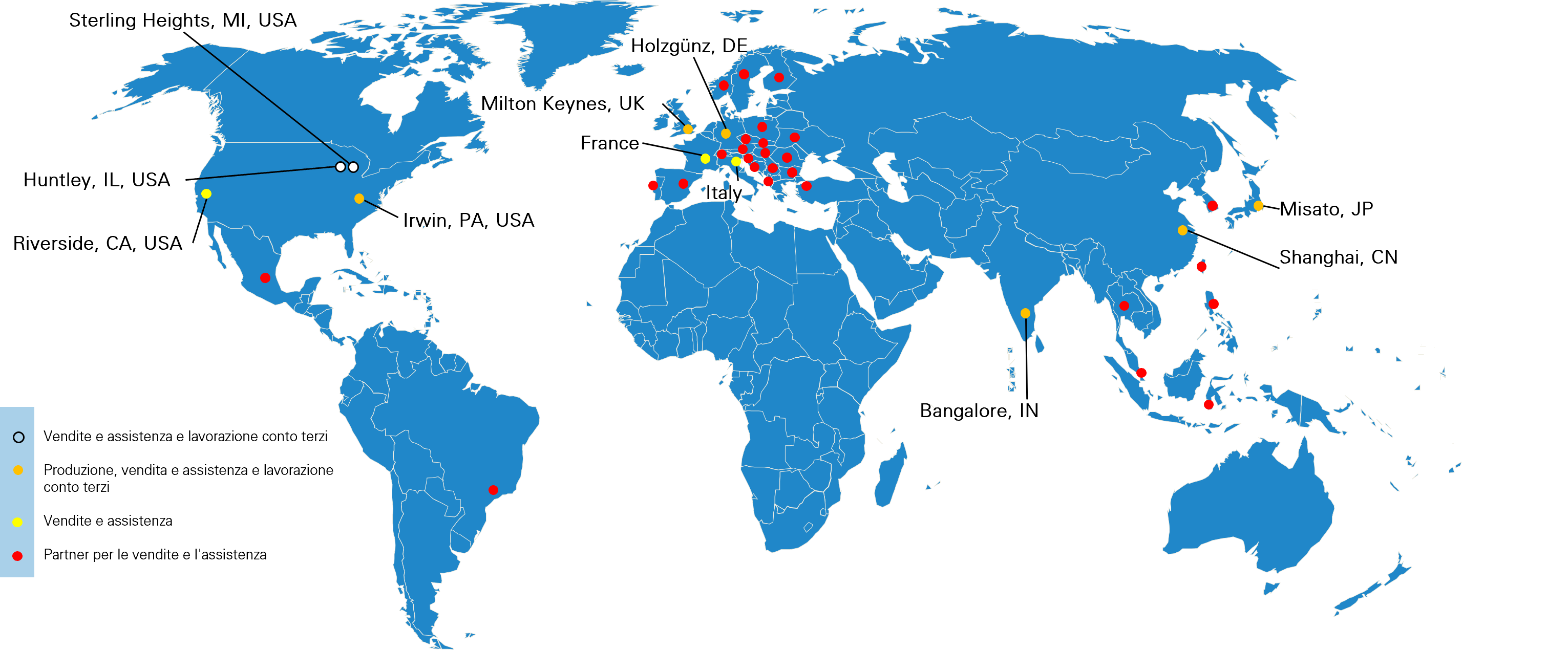