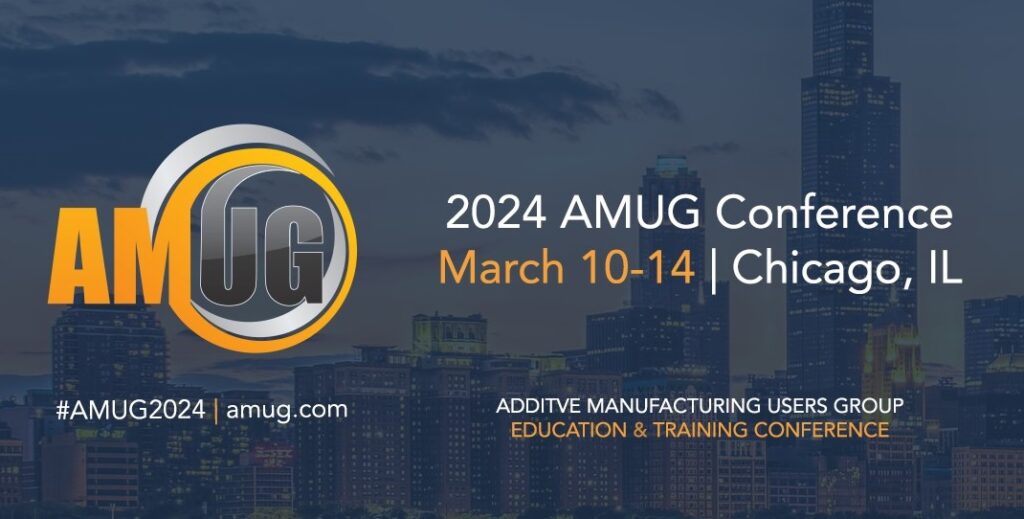
EXTRUDE HONE LE SOLUZIONI DI FINITURA AM ALL’AMUG 2024
Sarà inoltre presente con uno stand (stand numero 87 nel Salone D) dove i partecipanti potranno esplorare le loro tecniche di post-lavorazione di altissimo livello, come la Lavorazione a flusso abrasivo e la Lavorazione elettrochimica, che offrono capacità comprovate sul campo.
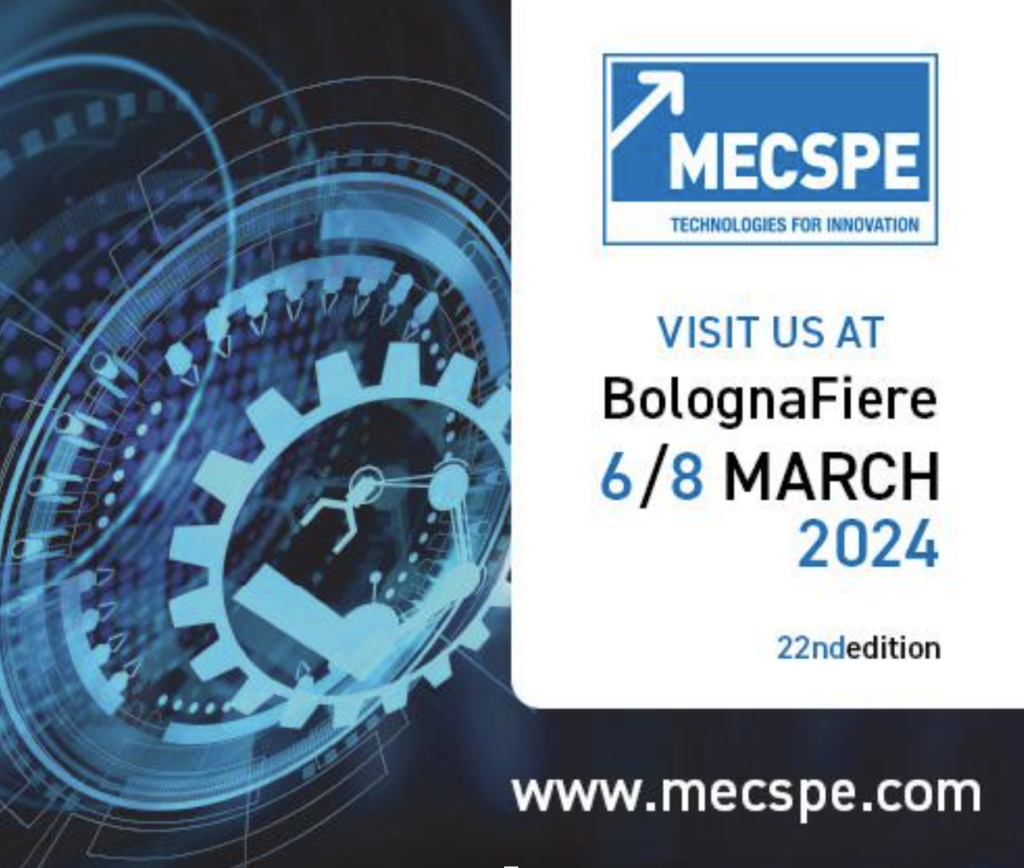
LE SOLUZIONI DI FINITURA AUTOMATIZZATE DI EXTRUDE HONE AL MECSPE
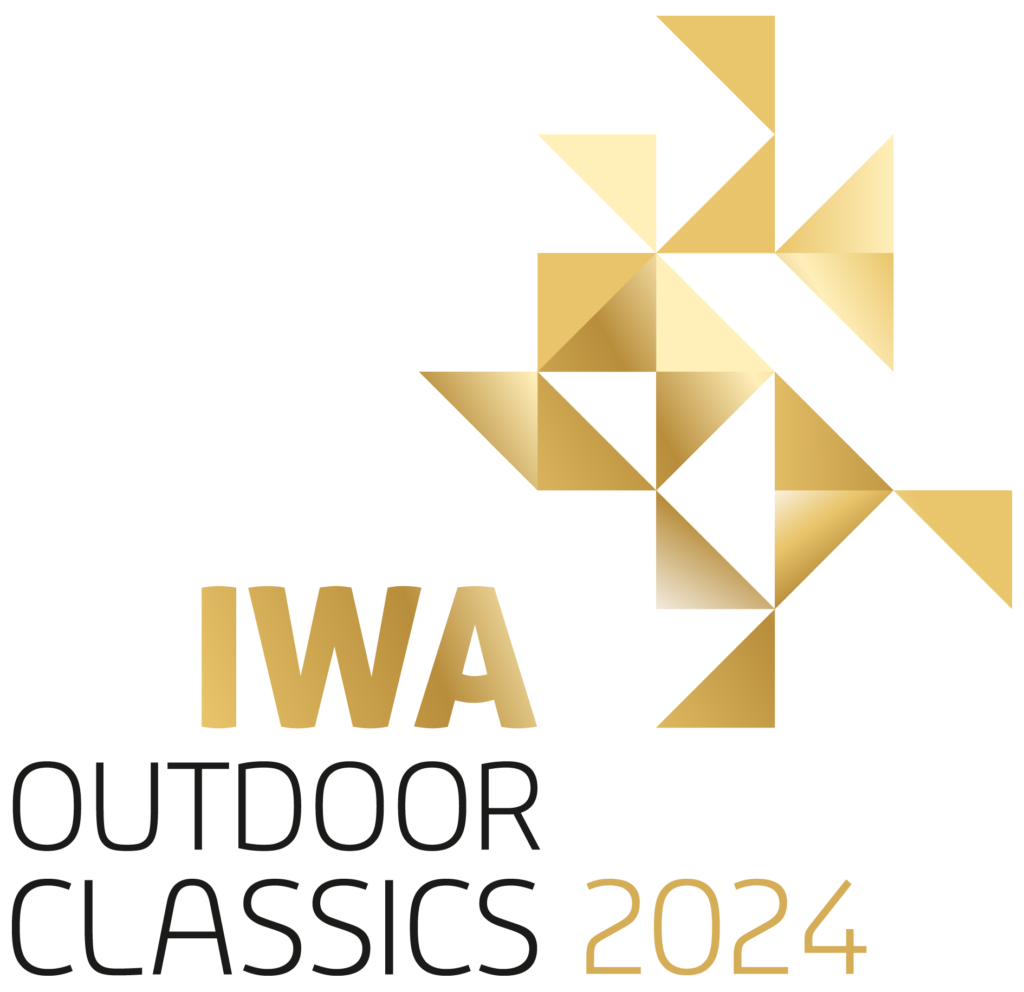
LA RIGATURA ECM DI EXTRUDE HONE OFFRE UNA SUPER PRECISIONE ALL’IWA
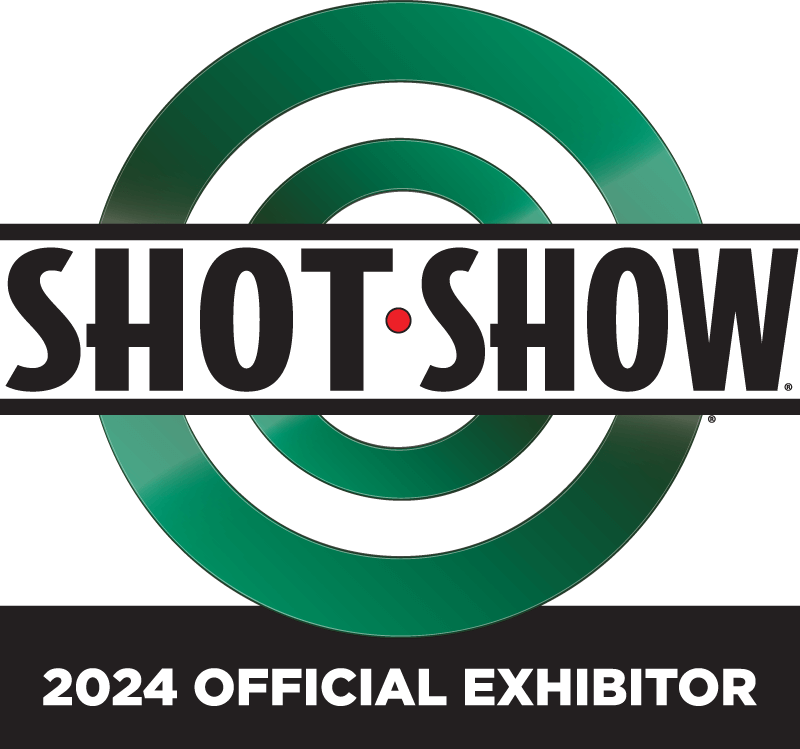
SOLUZIONI DI RIGATURA PERFETTE – SHOT SHOW 2024
Conoscete tutti il detto: Quello che succede a Las Vegas rimane a Las Vegas.
Noi di Extrude Hone siamo in parte d’accordo con questo detto. Ma ciò che scoprirete allo stand di Extrude Hone sarà oro puro che, secondo noi, porterete a casa e ne trarrete beneficio per anni.
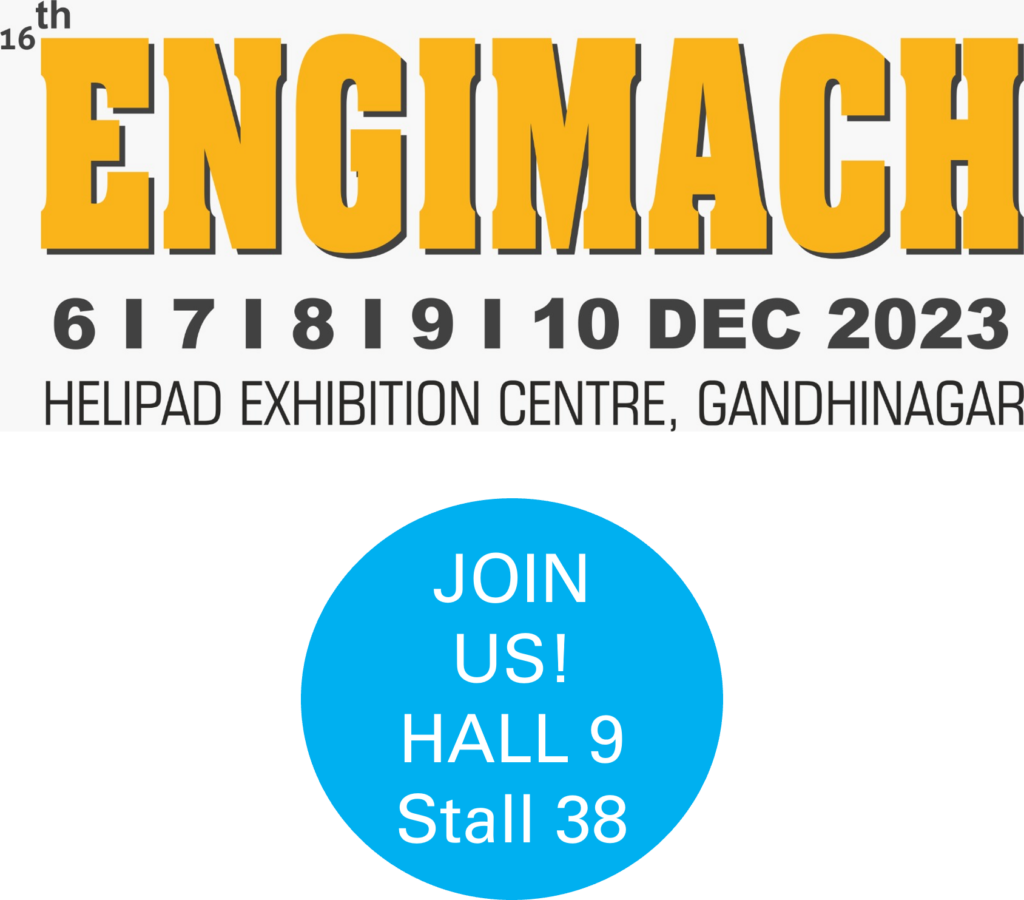
Preparatevi a incontrare il team di Extrude Hone India all’ENGIMACH.
Per quanto riguarda la finitura, Extrude Hone è con voi per aiutarvi a eliminare i punti critici.
(more…)
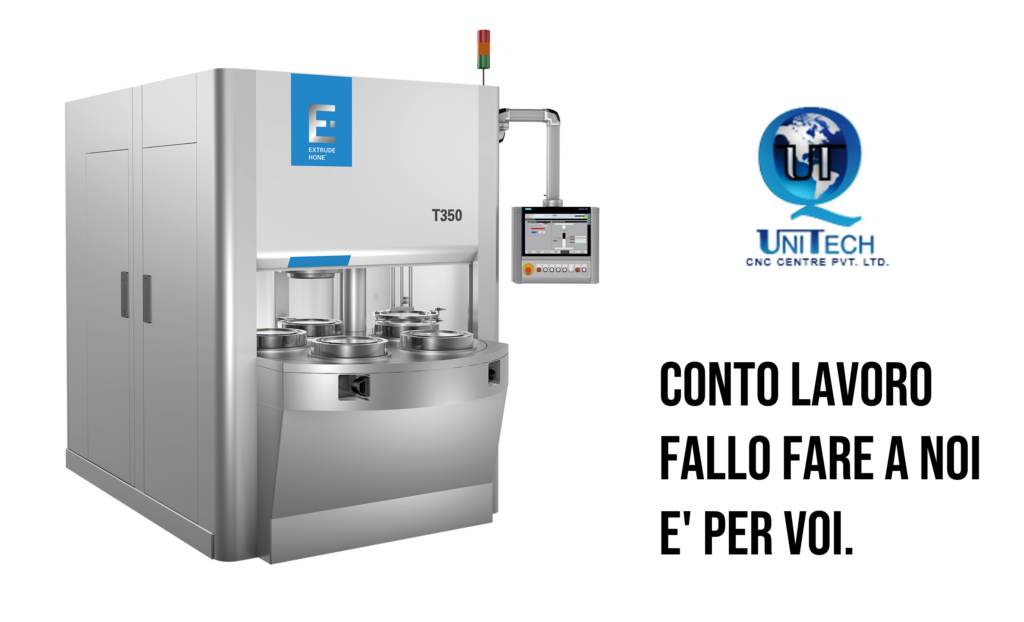
Sbavatura termica (TEM) in conto lavoro, testimonianza del cliente Unitech.
(more…)
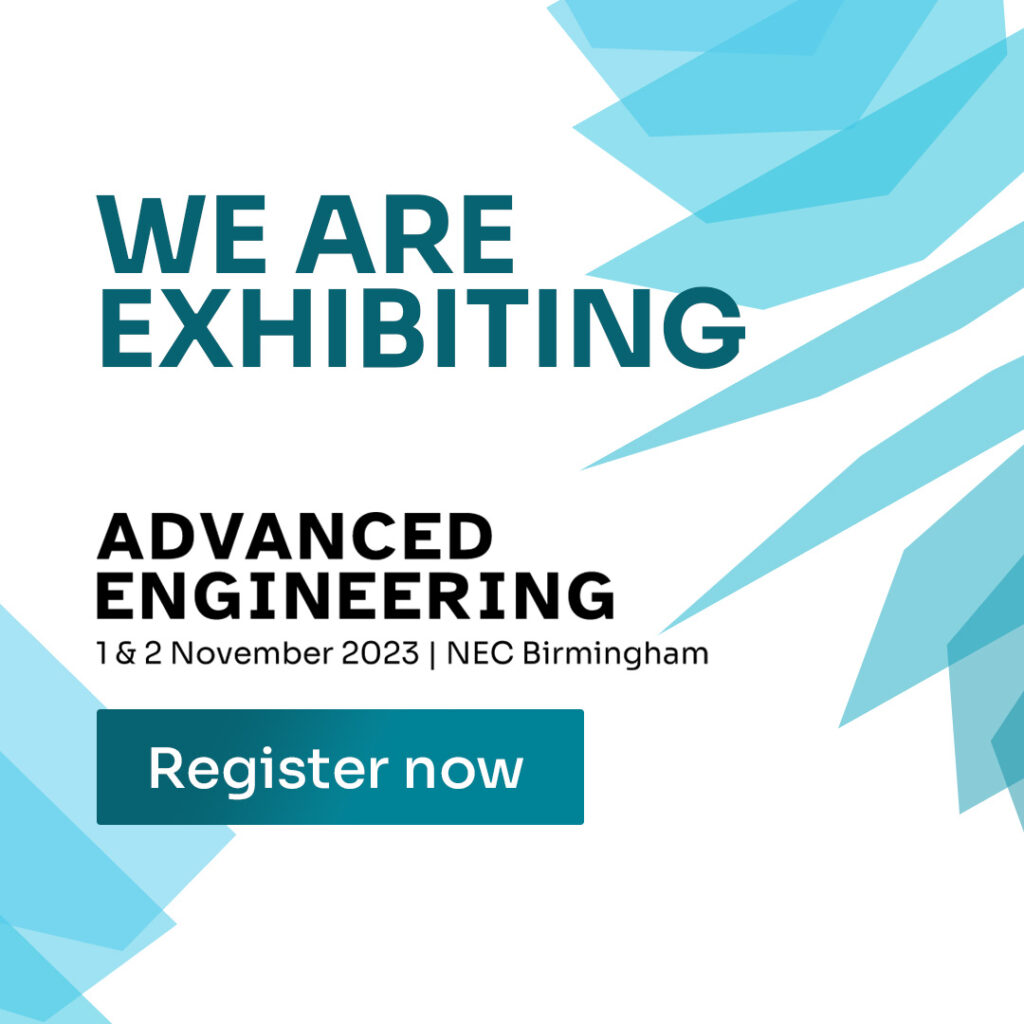
Advanced Engineering 2023
Oltre a un’ampia offerta, Extrude Hone Ltd è l’unico posto nel Regno Unito per i servizi di lavorazione a flusso abrasivo (AFM) in conto lavoro
(more…)