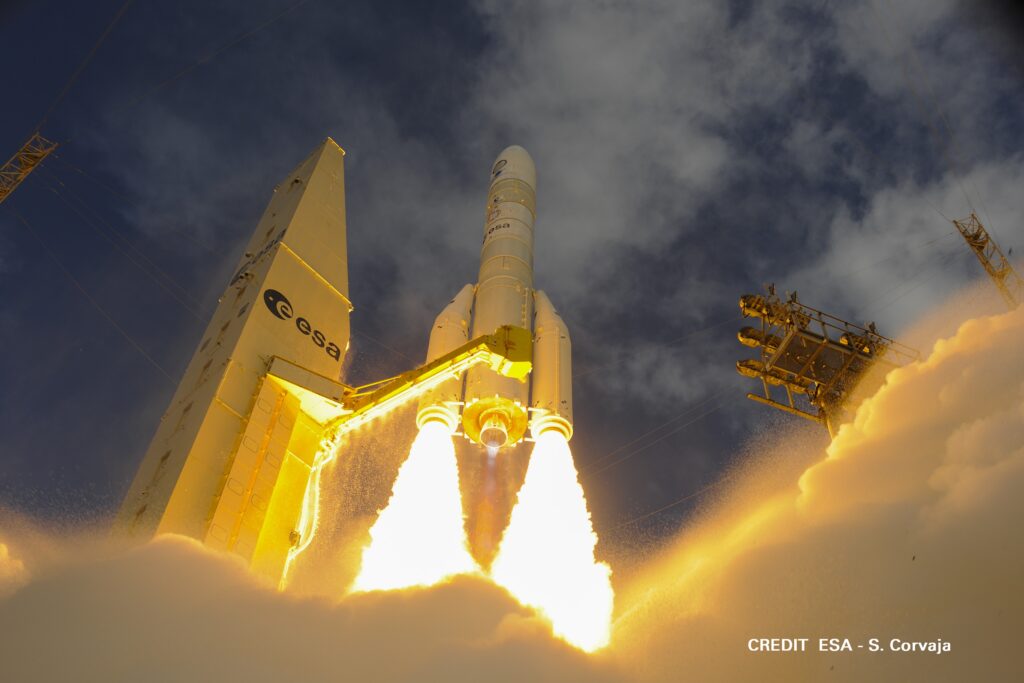
Extrude Hone saluta il successo del lancio dell’Ariane 6. L’Europa ha riconquistato l’accesso autonomo allo spazio.
È stato creato un team guidato da un esperto di metodi di finitura non convenzionali
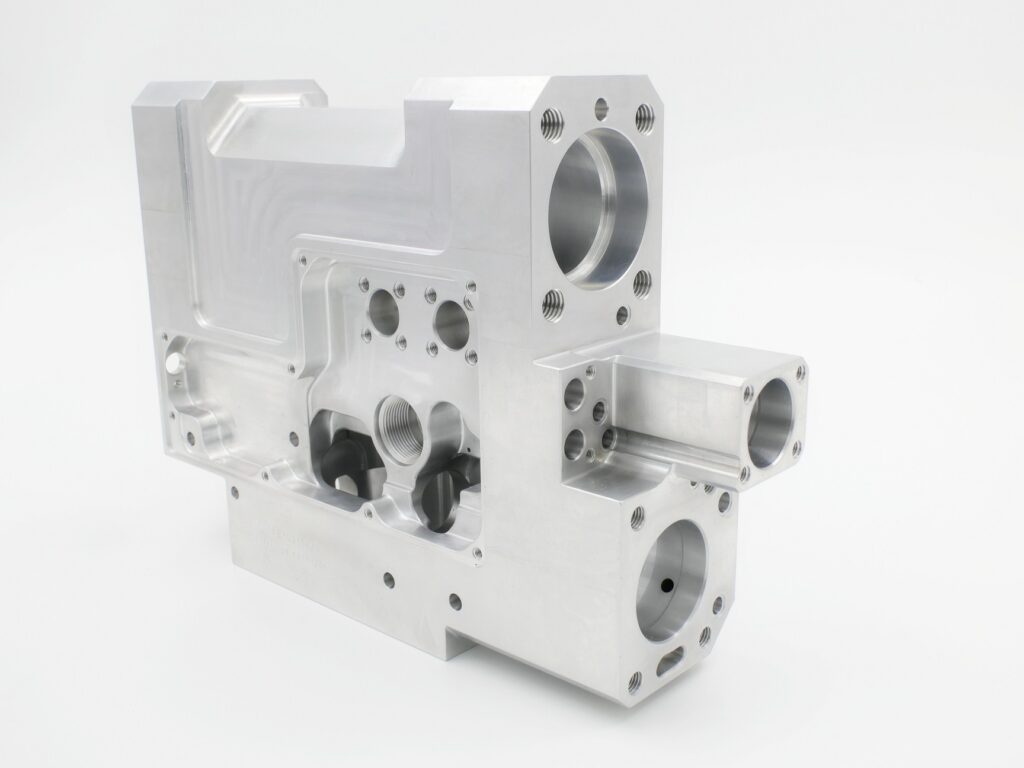
Il viaggio ispiratore di Siddhartha Sirdeshpande nella lavorazione elettrochimica (ECM).
Con un background nella lavorazione di precisione nei settori aerospaziale e automobilistico, Sirdeshpande ha parlato del suo percorso dall’automotive all’aerospaziale, evidenziando il ruolo centrale della tecnologia ECM. (more…)
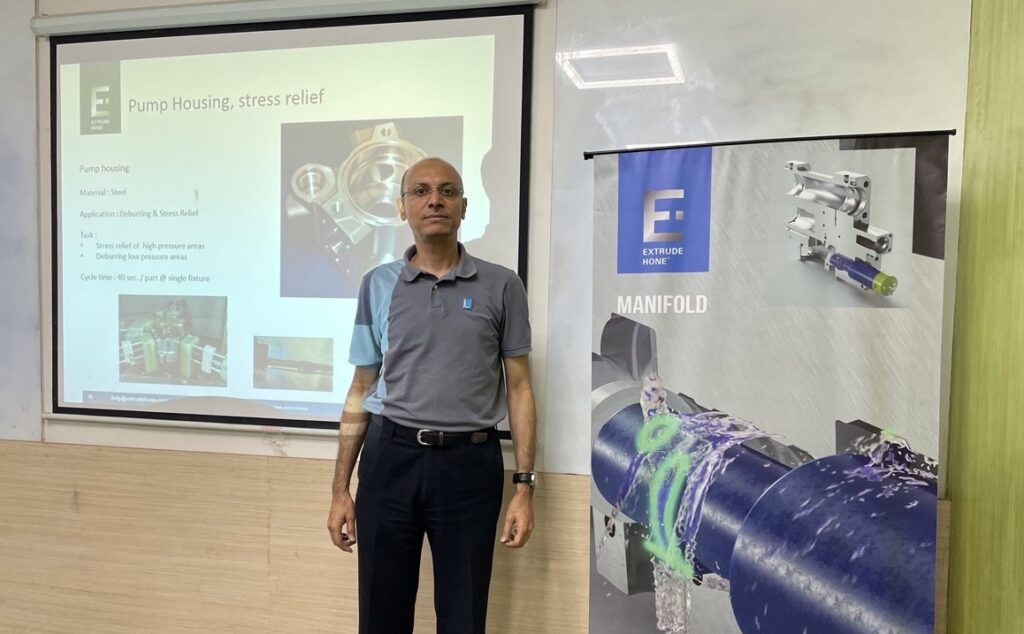
Extrude Hone offre la sua esperienza ECM e GST nell’ambito di un corso di formazione all’IMTMA
Tra i metodi di sbavatura più efficaci, due processi non convenzionali – la lavorazione elettrochimica (ECM) e la sbavatura termica (TEM) – sono soluzioni chiave per la sbavatura moderna.
Tuttavia, queste soluzioni chiave richiedono tecnici qualificati che devono essere formati da veri esperti, come quelli di Extrude Hone.
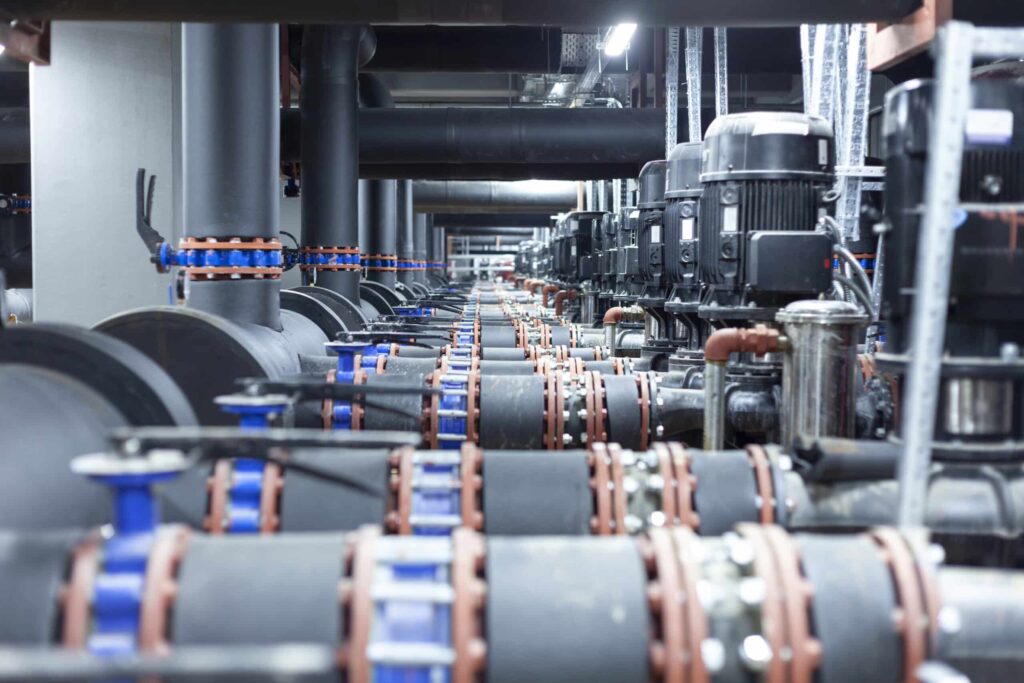
PICCOLE BAVE NEI COLLETTORI PORTANO A GRANDI PROBLEMI
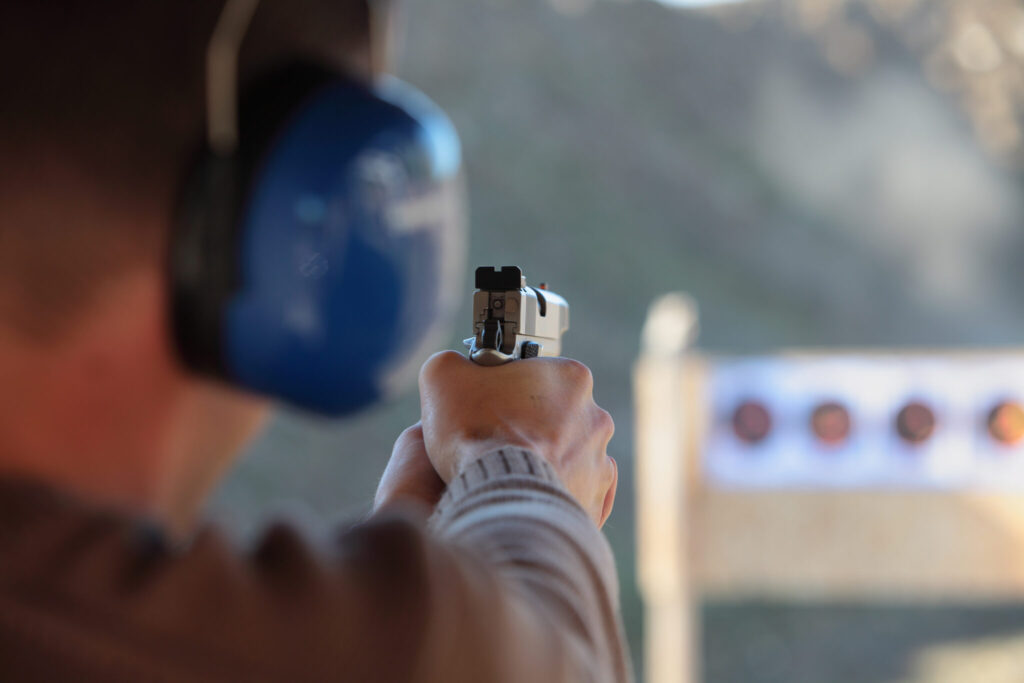
RIGATURA ELETTROCHIMICA: IL DIAVOLO SI NASCONDE NEI DETTAGLI
Questo articolo esplora le sfide della produzione di armi da fuoco e sottolinea l’importanza cruciale della rigatura per ottenere la migliore finitura possibile.
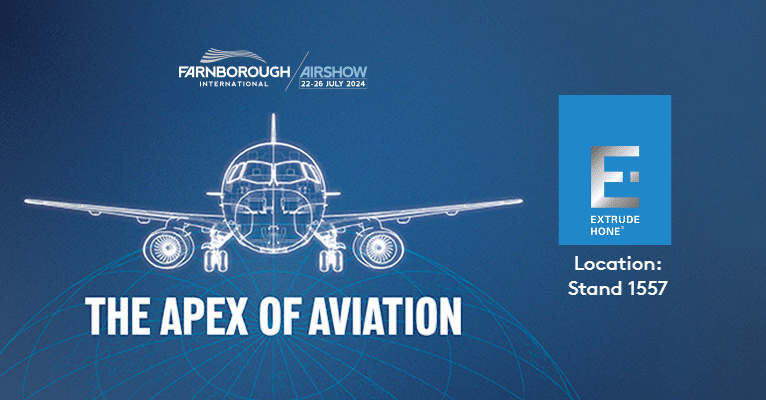
Le soluzioni di Extrude Hone per il settore aerospaziale al Farnborough International Airshow 2024
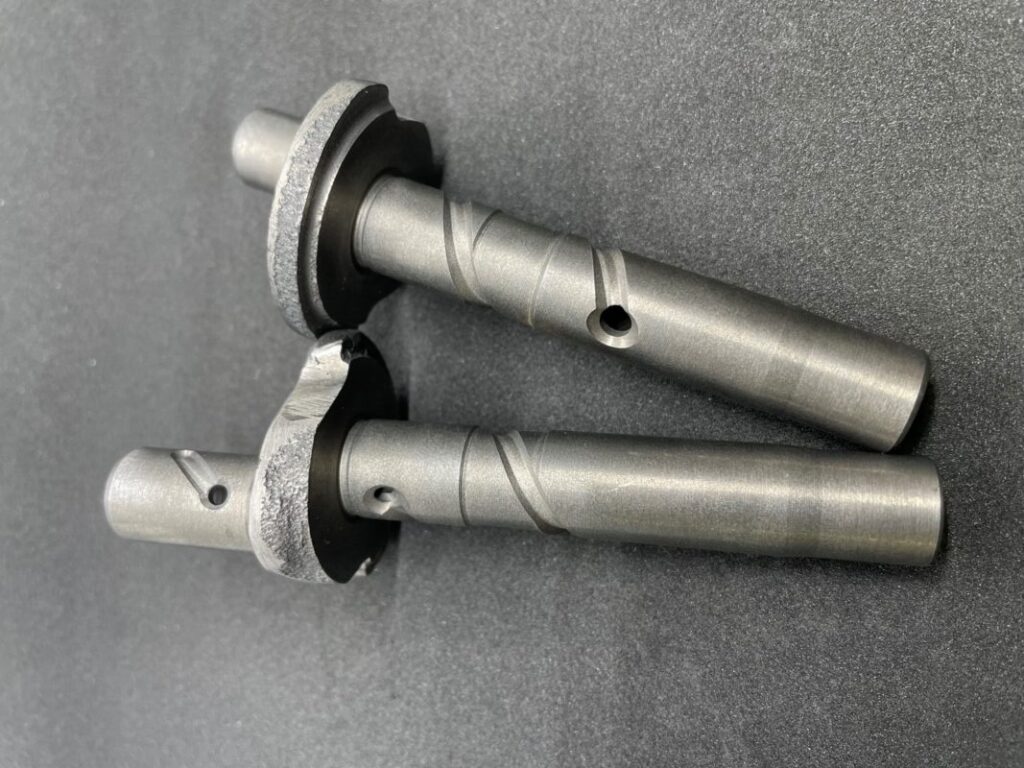
SBAVATURA TERMICA DELLA MANOVELLA DEL COMPRESSORE ALTERNATIVO
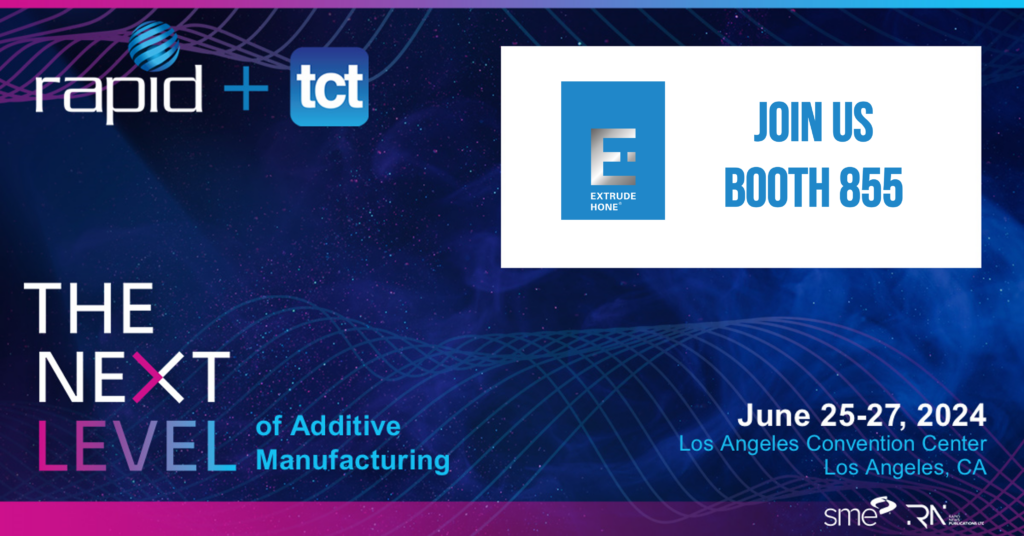
SOLUZIONI INNOVATIVE A RAPID + TCT 2024
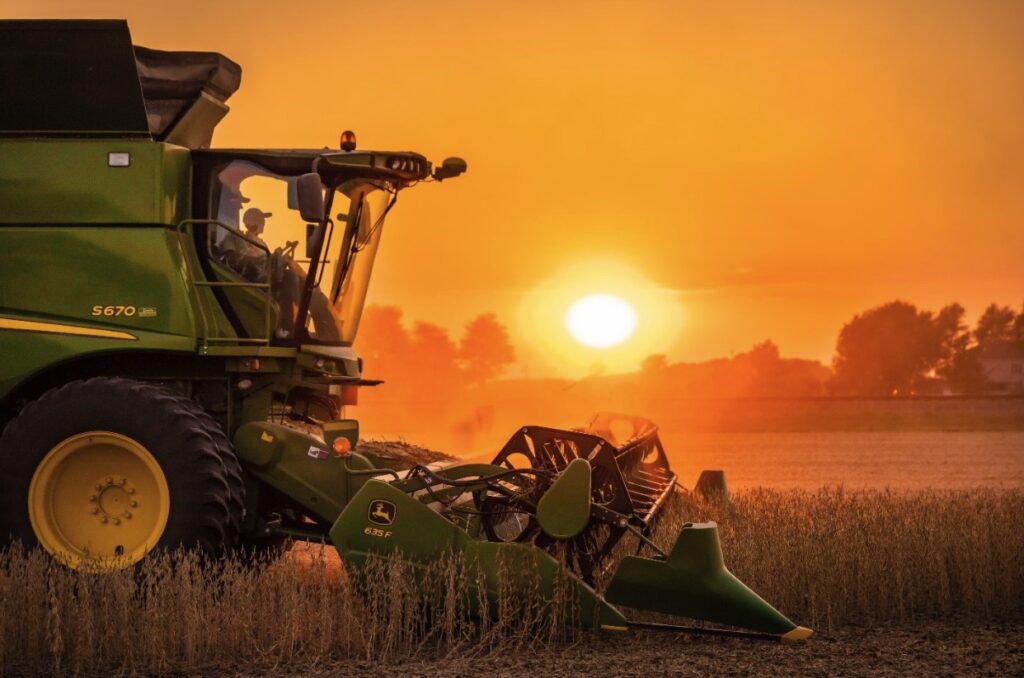
Extrude Hone intervista MINES sul suo percorso di sbavatura termica
Questo viaggio è tipico di ciò che molti clienti sperimentano quando iniziano con i servizi di contract shop di Extrude Hone prima di acquistare una macchina per proseguire la produzione interna.
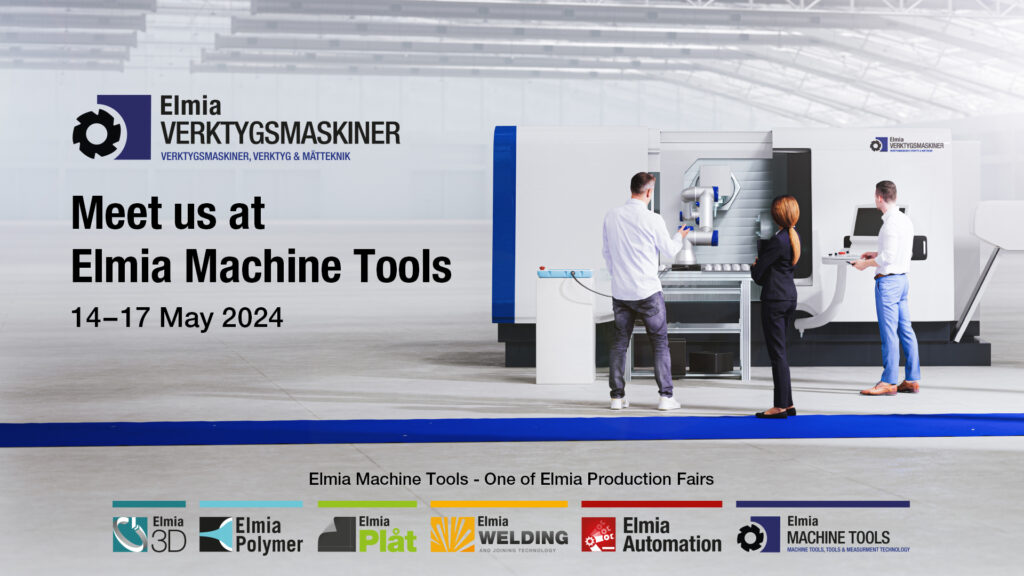
SOLUZIONI DI SBAVATURA E FINITURA EXTRUDE HONE AL ELMIA 2024 MACCHINE UTENSILI
Presso lo stand è possibile esplorare tecniche di post-lavorazione di altissimo livello, tra cui la sbavatura termica, la lavorazione elettrochimica (statica e dinamica), la lavorazione a flusso abrasivo e MICROFLOW, che offrono eccezionali capacità di sbavatura e finitura.