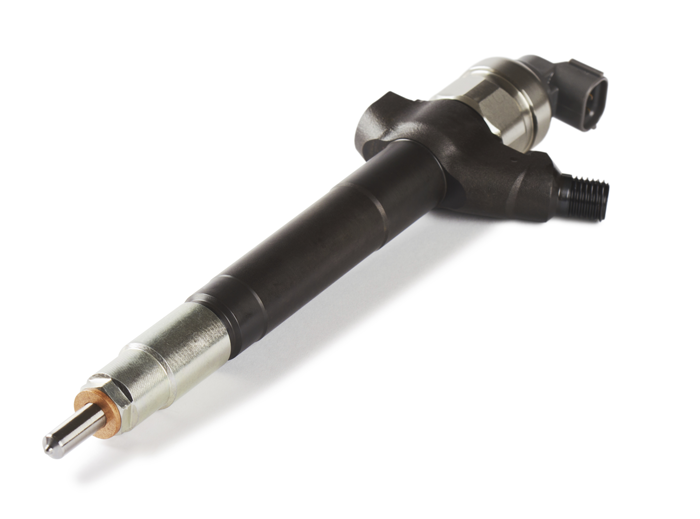
BURGMAIER HIGHTECH USES ECM TO PROVIDE THE EDGE
Radiusing & shaping solution for bore intersections at high-pressure areas of injector bodies. Absolute burr-free conditions by using ECM and thus achieves fatigue resistance in high-pressure components along with optimal efficiency due to enhanced flow properties. (more…)
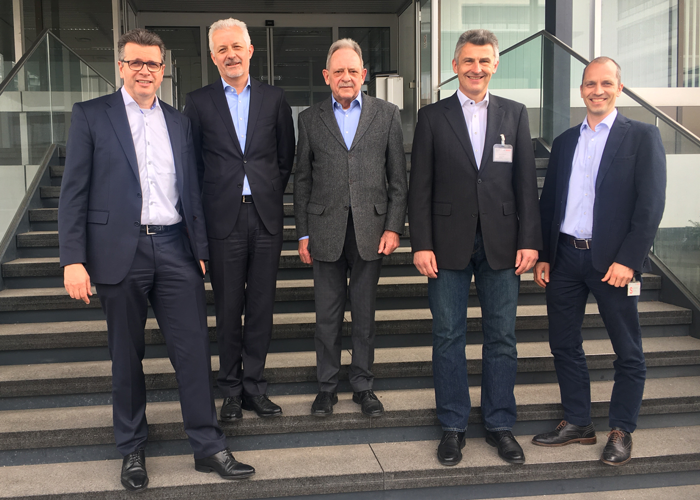
BOSCH REXROTH AG TRANSFERS TEM CUSTOMER SERVICE TO EXTRUDE HONE
Extrude Hone to take over the customer service for Bosch Rexroth AG TEM P80 and TEM P350. Bosch Rexroth AG has decided to transfer the entire customer service to Extrude Hone with effect from April 2nd, 2018. (more…)
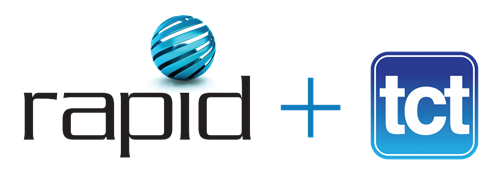
Extrude Hone at RAPID + TCT 2018
Patrick Matt from Extrude Hone to present at the RAPID + TCT
(Video) Another Great Video from CAMCRAFT!
Thanks #CAMCRAFT
Another great video from CAMCRAFT.
“Thanks Mike! I love to see happy customers promoting our technology. Extrude Hone invented Abrasive Flow Machining.”
(Video) ECM Electrochemical Machining for Fuel Injectors
Thanks #CAMCRAFT
Thanks Marc Bossert Great video, ECM Electrochemical Machining for fuel injectors, nice to see our machine and fixture (at that time we were Kennametal Extrude Hone see the sticker on the machine 0’17”).
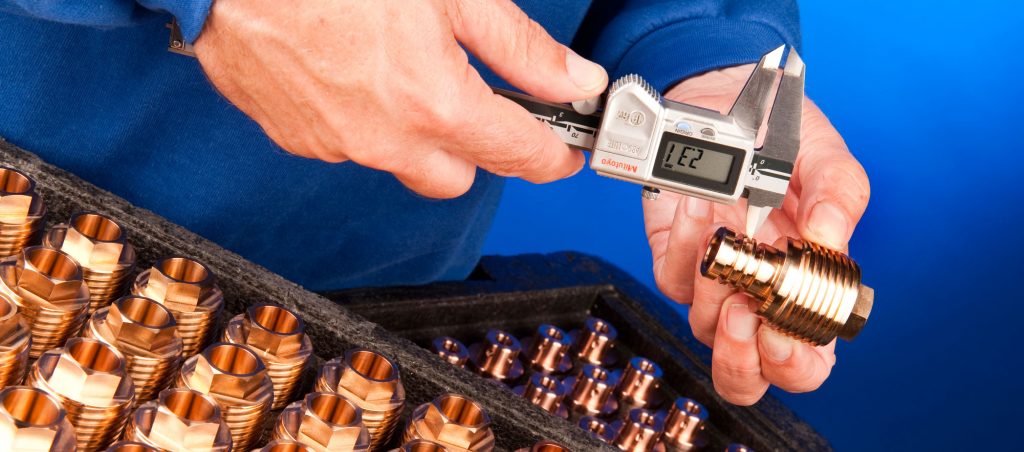
Parker Precision Limited trust Extrude Hone!
Parker Precision in UK use Extrude Hone contract shop capabilities to ensure burr free components. (more…)